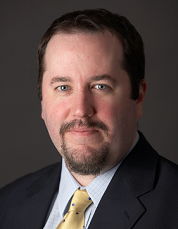
From global hotel operators like Hilton, Marriott and InterContinental Hotels Group to independent hoteliers like the Broadmoor, more hospitality professionals are using modular construction to open properties faster and meet green building goals.
“We believe the modular process will be a game changer for our valued development partners, especially during a time when labor shortages can be a challenge to timely openings,” said Karim Khalifa, Marriott International’s former Senior Vice President of Global Design Strategies. The company’s commitment to this building process is highlighted in its Modular Construction Initiative, which called for 50 hotel deals in 2017 to incorporate pre-fabricated bathrooms or guestrooms.
Modular Helps Get Heads in Beds Sooner
As KPMG’s “Smart Construction” report notes, “Many construction projects have a reputation for being completed behind schedule and over budget.” Hotel developers and owners throughout North America are experiencing this pain, especially considering severe shortages of skilled construction labor. To open properties more quickly, many of them are turning to off-site and modular construction.
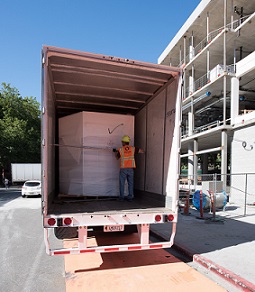
KPMG explains that off-site construction “offers a shortened and more reliable program,” with time savings of up to six months. Bathrooms are a prime beneficiary of modular efficiencies since building a typical bathroom requires 10 or more construction trades—including electrical, plumbing and finishing work ranging from dry wall and painting to mirror hanging. Because so many workers come and go in a small space, there’s a huge risk of damage to previously completed work. Bathroom rework accounts for about 60 percent of the punch-list in most hotel projects, and can cause weeks of schedule delays. Building with pre-fabricated modular bathrooms eliminates that risk.
Such bathroom pods are built off-site in a controlled factory setting, then trucked to the job site for “plug and play” installation. A prime example is the new 612-room Omni Louisville Hotel that opened in March 2018. Despite the city’s tight labor market, which is exacerbated by construction of 10 new downtown hotels, the project team was able to open the 30-story hotel a month earlier than originally planned. This experience is not unique, as we’ve seen similar—and even larger—time savings for hotels from Boston to L.A., and points in between.
Green Benefits of Modular Bathrooms
While developers typically decide to use modular bathrooms for the time savings and improved quality, pre-fabricated bathroom pods also offer several green benefits. Chief among these are:
- Reduced material waste;
- Improved air quality; and
- Greater energy efficiency.
Reduced Material Waste
The largest green building benefit of using modular bathrooms is reduced construction material waste—in the short-term during initial construction and in the long-term during hotel remodels and upgrades.
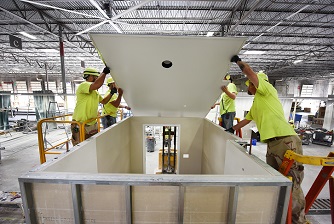
Short-term—Because modular bathrooms are built in a factory setting, materials can be better planned and optimized than on a job site. Precision manufacturing allows for ordering just the right amounts of materials and optimizing cuts to help eliminate scrap. Additionally, any cut-offs generated can be carefully tracked as inventory and used in other projects.
Building bathroom units in an indoor, climate-controlled environment also eliminates material damage and loss from exposure to environmental conditions.
As the factory can purchase materials like toilets and mirrors in bulk, there also is much less packaging to dispose of than occurs with site-built bathrooms. Types of materials reduced range from cardboard and protective foam to shrink wrap and wood pallets.
The result of all these factors is much less waste going to landfills during hotel construction.
Long-term—In addition to reducing material waste during initial construction, high-quality pre-fabricated modular bathrooms help hotel owners reduce waste over the long-term during property upgrades and remodels. For example, Oldcastle SurePods manufactures its bathroom pods using durable materials like a patent-pending, fully waterproof and crack-proof ceiling, and USG Fiberock Aqua-Tough interior panels. Such materials provide a solid foundation for future bathroom upgrades and eliminate the need for drywall replacement.
A case in point is the recent remodel of a Courtyard by Marriott in Hagerstown, Maryland. Originally built with modular bathrooms, after seven years and an average 2,000 guests per room, there was no mold or water leaks in any of the hotel’s 100 guestroom bathrooms. “The bathrooms really have held up well; we didn’t have to remove any drywall—there’s no damage, mold or things we find all the time [in a conventional bathroom remodel],” said Gary Fennell, Director of Facilities and Construction for hotel developer and manager Plamondon Hospitality Partners. Not needing to replace drywall not only reduced scrap from the remodel, it also helped reduce labor time. Fennell notes he was able to shave about two days off the renovation for each of the property’s floors.
Improved Air Quality
One surprising green building benefit of modular bathrooms is their role in improving air quality by reducing the potential for harmful molds. The Modular Building Institute explains that modular construction can improve indoor air quality because: “The modular structure is substantially completed in a factory-controlled setting using dry materials, [so] the potential for high levels of moisture being trapped in the new construction is eliminated.”
Greater Energy Efficiency
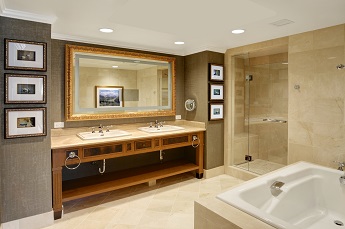
Due to precision construction, modular bathrooms also can help contribute to a more airtight, energy efficient building. Les Bluestone, Partner of Blue Sea Development Co., experienced this first hand when building the Prospect Plaza housing project in New York City. To meet energy efficiency targets for the project under several green building programs (Energy Star, National Green Building Standard and LEED) the Prospect Plaza project team needed to meet airtightness requirements between individual apartments and the exterior. “The [SurePods] bathrooms passed the airtightness requirement better than anything that could have been field constructed,” said Bluestone.
Additional Green Building Benefits
Depending on the bathroom pod manufacturer, additional benefits of these units include:
- Use of recycled steel and gypsum board;
- Energy-efficient LEDs;
- Water-conserving fixtures; and
- Low VOC or no VOC adhesives and grouts.
Conclusion
While using modular construction in your next hospitality project might help you start earning some “green” earlier through opening your property sooner, if a green reputation is important to you, modular also can help you be a good environmental steward.
Bill Seery is Director of Business Development for Oldcastle SurePods modular bathrooms. Seery has specialized in the building prefabrication industry for more than 10 years, with responsibilities for both management and operations. A winner of the Shingo Prize for Operational Excellence, he holds a BS in Industrial Engineering from University of Massachusetts, Amherst, and an MBA from Bentley University. Contact Seery at Bill.Seery@oldcastle.com.