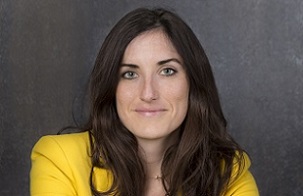
As sustainability becomes a priority for global businesses, the manufacturing and construction industries are turning to more eco-friendly solutions. This is especially the case for surfacing materials.
Sustainable manufacturing driven by new technology and streamlined production processes is changing the way we look at materials for the built environment. It’s actively encouraging better practice in the construction industry. Residential and commercial projects benefit from new techniques and approaches to building, including retrofitting and refurbishing, and offsite production and prefabrication.
These modern methods directly contribute to green initiatives, cutting costs and supporting society, raising an opportunity to train a new workforce and increase employment. Using sustainable materials, particularly for surfaces, also increases long-term value and extends the lifespan of a building.
Here, we present some of the ways in which production methods can be improved for the betterment of both society and the environment:
Innovation is Key
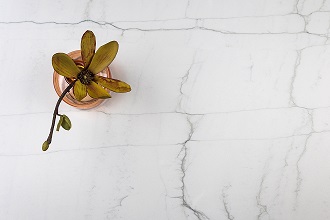
Technological innovation is driving surfacing manufacturers to become more sustainable in their practices. Manmade materials are now actively helping to rebuild the environment as opposed to detracting from it.
Through manmade creations, the environment can begin to rebuild itself, and companies save on production costs in the process.
Sintered stone is a technological innovation that has positively changed the global surfacing industry, sending shockwaves through the natural stone industry. The 100 percent recyclable and environmentally friendly product is made from organic raw materials which are subjected to very high temperatures and pressure, replicating the thousands-of-years process of natural stone creation in just a few hours.
It’s not just the composition of the surfaces but the design too. New decoration technologies also contribute to a concerted effort to protect the environment. One recent example is our own HYDRO-NDD 2.0, which uses water-based inks rather than the solvent reliant variations to reduce CO2 emissions.
Consolidate Production
Manufacturers are also looking at how they can better source raw materials. One way is to consolidate production processes, which helps to reduce costs and guarantee the material’s quality and reduces CO2 emissions and environmental damage from transportation.
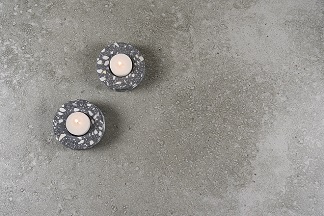
Like many others in the building materials manufacturing industry, we are constantly seeking new ways of consolidating our physical assets and obtaining direct control of our raw material. This will help us to meet a rapid increase in global demand for sintered stone surfaces and ensure consistency in the quality of our product.
Don’t Start from Scratch
Looking to the construction industry, the process of retrofitting and refurbishing is an important sustainable option quickly growing in popularity. Since 1990, gross U.S. greenhouse gas emissions have increased by 1.3 percent. In 2017, around 22 percent of these were caused by nationwide burning of fossil fuels for energy and chemicals released from raw materials during the production of goods.
Designing-out old, non-sustainable materials and replacing them with sustainable ones creates more energy efficient, “high-performance” buildings. This means the retrofitted building lasts longer, costs less to operate, increases in value and supports a better quality of life.
Build it Offsite
There are many advantages of prefabricating the materials for a project in an offsite location, including energy reduction, waste minimization and increasing the longevity of the material.
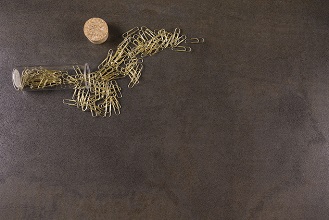
When the assembly process takes place in an offsite setting, it shortens the time it takes to create individual parts, which means less energy is used. As each component of the building’s construction is assembled from the start, waste material is also reduced and the quality of the project is consistent. Further, prefabricated components are easier to dismantle and relocate to different sites, and are given a second life once a building is no longer in use.
Focus on Value
Sustainable manufacturing is valuable for both the manufacturer and the community.
The steps manufacturers take when they implement sustainable methods relieves environmental pressures and reduces their carbon footprint, but also cuts costs and benefits society.
Green surfacing materials such as sintered stone are growing in popularity among architects, designers, project managers and homeowners. At Neolith we are committed to sustainable practices and implement a variety of green techniques and technologies in the creation of our product to help protect the environment and continue to deliver a superior product to our broad base of clientele.
Mar Esteve Cortes is Director of Neolith.