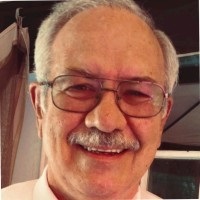
Energy consumption in the hotel industry is high, even when compared to other commercial sectors such as hospitals and schools. The truth is hotels and motels make for inherently energy-intense buildings, primarily due to the nature of the business and guest behavior. As such, hotel management is always seeking ways to maximize efficiency and save energy (and thus money) while, at the same time, providing optimal comfort for occupants. Many hotels are investigating environmentally friendly technologies that have the potential to reduce energy usage. Time after time, the primary technology that comes out on top is geothermal heat pumps. The reason is they consume significantly less energy and are at least three to four times more energy-efficient conventional heating and air conditioning systems. According to the peer-reviewed scientific publication, Journal of Cleaner Production, hotels with heat pumps use nearly 20 percent less kWh/m2 than hotels with district heating.
Water source heat pumps used for geothermal applications work by using energy from the ground or surface water to heat and cool buildings. They are highly efficient and can provide significant savings on heating, cooling and hot water costs compared to traditional systems. Water source heat pumps have three main components: a compressor unit, an evaporator coil, and a condenser coil. The compressor is responsible for moving refrigerant between the evaporator and condenser coils to create a cooling or heating effect. The evaporator coil is located outside of the building and absorbs heat from the ground or water source. This heat is then transferred to the refrigerant inside the compressor unit. The compressor pushes the gas molecules together, heating them up as the pressure rises. Finally, the compressed refrigerant is passed through the condenser coil located inside the building. This coil then releases heat into the building, providing either cooling or heating depending on what season it is and what type of system has been installed.
Just like how regularly changing the oil in a car will help increase the “shelf life” of the car, regular maintenance will help keep heat pumps running at peak efficiency for years on end. That said, because HVAC systems are used more frequently—and at more extremes than other commercial systems throughout the year, it is critical to provide them with regular maintenance and a thorough inspection and cleaning at least twice per year. The best times for this are during changing of the seasons in winter and summer.
Maintenance Tips for Water Source Heat Pumps
- Filter changes or cleaning are required at regular intervals. The time between filter changes will depend upon the type of environment where the equipment is used. In applications such as hotels and motels, daily vacuuming can put a large amount of lint and dust in the air, and filter changes may be needed as frequently as bi-weekly. Conversely, in a single-family dwelling, replacing, or cleaning the filter every 60 days is sufficient.
- An annual summer and winter “checkup” are recommended by a licensed service professional. Recording the performance measurements of volts, amps, air temperatures and water temperatures is recommended. This data should be compared to the information on the unit’s data plate, the data recorded at the original startup of the equipment, and the performance information provided by the manufacturer at or near commissioning or testing conditions.
- During either season annual “checkup”, if electrical problems are indicated, it is recommended to check volts, amps, and resistance of components to determine if connection or component issues exist. Faulty electrical components should be replaced as necessary, and proper electrical flow should be verified.
- During either season annual “checkup”, if air flow problems are indicated, it is recommended that air flow volume be determined and adjusted as necessary by blower speed or interface board adjustments to match manufacturer’s rated air flow for the unit during the cooling and/or heating mode. Air coils should be checked as well and cleaned with a commercially available coil cleaner if necessary. It is important to use the right chemical cleaner, one that is specifically designed for coils. Using the wrong cleaner could damage the coil.
- During either season annual “checkup”, if waterside problems are indicated, checking temperature difference and pressure drop across the coaxial coil is recommended to determine gallons per minute of water flowing and capacity versus manufacturer’s specifications at similar conditions. A pressure gauge and temperature analyzer are recommended for collecting readings. Applying the data to industry-related formulas and calculations will indicate whether further water/fluid issues exist, such as heat exchanger problems, fluid volume problems, or fluid flow problems. This checkup can also indicate possible refrigerant problems if the fluid checks are not directly responsible for issues.
- During either season annual “checkup”, if refrigerant problems are indicated, checking superheat and subcooling is recommended to determine the level and location of existing liquid refrigerant (“charge”) in the refrigerant circuit. Use of a pressure and temperature chart matching the unit’s refrigerant type may be required to properly guide the technician to either refrigerant circuit components or charge level issues. If necessary, refrigerant circuit components may need replacing, or the refrigerant charge level may need adjustment based on industry-accepted procedures.
- Lubrication of blower motors is typically not required.
- The condensate drain should be checked annually by cleaning and flushing to insure proper drainage.
- Periodic lockouts are almost always caused by air flow problems. The lockout (shutdown) of the unit is a normal protective measure in the design of the equipment. If continual lockouts occur call a mechanic immediately and have them check for air flow problems or air temperature problems.
Water source heat pumps have a low environmental impact due to their reduced electricity consumption and emissions. When properly cared for, heat pumps are highly adaptable to changing weather conditions, meaning they can provide consistent performance throughout the year—and for many years to come.
About the Author
Phil Rains is an application engineer and trainer for Bosch Thermotechnology with a focus on commercial water source/geothermal heat pumps. He has over 50 years of experience in the HVACR industry.