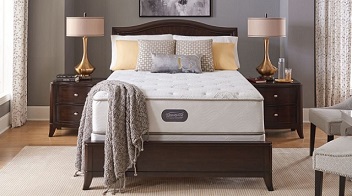
NATIONAL REPORT—Tempur Sealy International (Tempur, Tempur-Pedic, Sealy featuring Posturepedic Technology, and Stearns & Foster) calls itself the world’s largest bedding provider. Serta Simmons Bedding (Serta, Beautyrest, Simmons, and Tuft & Needle) calls itself North America’s largest bedding manufacturer. Undoubtedly, the U.S. lodging industry gets a significant share of its mattresses and box springs from these companies. Can these companies be considered leaders in sustainability? Green Lodging News reached out to both companies for interviews without success. A Tempur Sealy International representative provided the company’s January 2020 Corporate Social Values report and a Serta Simmons Bedding representative provided a link to a Serta Hospitality Sustainability website page.
According to the 17-page Tempur Sealy International (TSI) report, it is the first such report for the company. It divides its sustainability commitment into three areas: Purpose, Our People, and the Environment.
Environment
TSI says it has partnered with Northstar Recycling to help track waste and recycling, reduce its waste, and increase recycling in most of its manufacturing facilities, distribution centers, and corporate offices in the United States.
“We strive to achieve zero landfill waste at each of our foam manufacturing facilities and are proud to report that we have either achieved this goal or nearly achieved this goal at two such production plants in each of the last few years,” TSI says. “We currently recycle materials such as cardboard, wood, foam, steel, plastic, textiles, and aluminum and continue to evaluate additional recycling opportunities. We have a scrap management program to assist teams at each of our facilities with waste reduction efforts.”
In 2019 TSI recycled 85 percent of the waste from all of its North American facilities. TSI has partnered with the Mattress Recycling Council, which is a member of the International Sleep Products Assn., to participate in the Sleep Products Sustainability Program (SP2) in its Richmond and Los Angeles production plants. TSI is ISO 14001 certified at three of its four foam manufacturing facilities.
TSI’s foam manufacturing facility in Duffield, Va., met the Energy Star challenge in December 2019. The Duffield team committed to a 10 percent energy reduction program over a five-year period and has achieved a 37 percent reduction in energy consumption per pound of chemical processed since 2015.
In 2012, TSI’s Mountain Top, Pa., facility invested in its internal waste water treatment plant to effectively purify the water that results from production processes. From 2013 through 2019, this waste water treatment process has resulted in the reduction of greenhouse gases by 2,900 metric tons of CO2 emissions and in the processing of 27 million gallons of water to the point the water can be safely returned to the natural water cycle through the local publicly owned treatment works.
Additional TSI Accomplishments
All three of TSI’s foundation base lumber suppliers are Sustainable Forestry Initiative (SFI), Forest Stewardship (FSC), or Canadian Standard Association (CSA) certified.
TSI is currently transitioning to energy-saving LED lighting in all of its production and assembly facilities. At present, approximately 70 percent of its facilities in the United States utilize LED lighting.
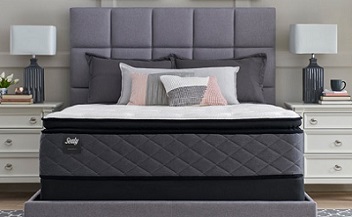
TSI’s corporate headquarters building is LEED certified.
TSI is continually looking at methods to improve its delivery operations through optimizing delivery routes, reconfiguring truck cube utilization, combining Tempur and Sealy products for delivery in the same truck, and co-locating manufacturing facilities and distribution centers for Tempur and Sealy products whenever feasible.
In the past, TSI shipping containers were comprised of two full corrugated cardboard boxes with one nested inside of the other in order to increase the containers’ strength. TSI now uses a single-wall box with corrugated cardboard inserts in the corners, which enables TSI to obtain the same stacking strength with approximately 45 percent less cardboard material.
High Percentage of Recycled Steel
Innersprings used in the Sealy Response, Hybrid and Stearns & Foster products are manufactured using approximately 99 percent recycled steel. TSI’s new product development center in Trinity, N.C., recycles all the mattresses it uses in testing, thus reducing the waste stream by approximately 2,000 mattresses annually.
The TSI product lineup now includes compressed mattresses. By compressing mattresses into smaller sizes before shipping, TSI can reduce the amount of product packaging and reduce fuel usage and greenhouse gas emissions associated with transportation operations.
Many of TSI’s mattresses and foams are green certified by international organizations.
Since 2011, the company has donated more than 200,000 mattresses to charities.
TSI has a Code of Business Conduct and Ethics and a Supplier Code of Conduct.
Serta Simmons Bedding
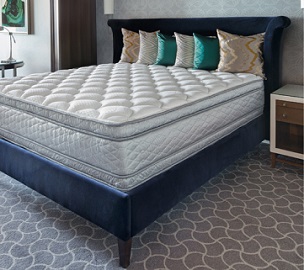
If you go to the Serta Simmons Bedding website, you can learn a bit about how the company ensures efficiencies in its operations. For example, all Serta Simmons Bedding work is done in North America, supporting local manufacturing. There is little to be found there, however, in the area of sustainability. If you dig down into the company’s website and check around, there is much more information.
According to the Serta site, 100 percent of Serta innersprings and box springs are made from 95 percent post-industrial recycled steel. Many of the fabrics used in Serta mattress covers meet the STANDARD 100 by OEKO-TEX for manufacturing without the use of harmful substances, including cover fabrics made from natural bamboo and/or pure organic cotton.
Serta uses latex made from a natural/synthetic latex blend that is naturally anti-microbial and allergen resistant. It is made to the STANDARD 100 by OEKO-TEX level for manufacturing without the use of harmful substances.
All of Serta’s foams are made without the use of PBDE flame-retardants, CFCs, lead, mercury, prohibited phthalates, and other potentially harmful materials. Soy-based foams are used in multiple product lines.
Serta’s fire-retardant barriers are made primarily from cotton or other cellulosic renewable fibers and use no harmful chemicals or processes.
All Serta insulator pads are made from virgin recycled garment clips.
Efficiency in Manufacturing
All remnant scrap of mattress ticking, foam, wood, steel, and plastic is recycled. All crating materials for innersprings are recycled. Serta mattress plants and suppliers are located near customers to minimize transportation costs and fuel consumption. The company has reduced secondary packaging to less than 5 percent of product weight. All Serta products are manufactured on a “Just in Time” schedule, reducing unnecessary energy use, minimizing waste, and allowing for less warehousing.
On its Tuft & Needle website, Serta Simmons Bedding says, “We were the first complete mattress to be certified STANDARD 100 by OEKO-TEX and hold more certifications than most of our competitors.”
Tuft & Needle dedicates a section of its site to its philanthropic efforts. “Through our return policy, direct product donations, and school fundraising program, we’ve donated over $9m in mattresses back to the community,” the website says.
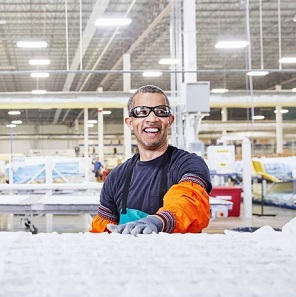
Simmons Beautyrest Hospitality Bedding
At the Simmons Beautyrest Hospitality website, there is a section dedicated to sustainability.
“At Simmons Beautyrest Hospitality Bedding, sustainability is not simply an initiative,” the company says. “It’s a defining characteristic of how we do business. From product development and manufacturing to logistics, we adhere to the principles of sustainability in virtually all aspects of our operations.”
All Simmons Beautryest Pocketed Coil springs contain recycled steel. The company also uses CertiPUR-US certified foams, which means they don’t contain ozone depleters; PBDEs, TDCPP or TCEP flame retardants; formaldehyde, mercury, lead and other heavy metals and have low VOC emissions for improved indoor air quality. Many of the fabrics used in mattress production are derived from cultivated wood fibers and the wood used in EnduroTECH foundations is sourced from sustainable forests and is 100 percent recyclable at the end of its useful life.
“Our plants are strategically located to minimize the use of fuel and energy in shipping to hotel customers worldwide,” the website says. “Our mattress reclamation and recycling initiatives have helped divert more than 2 million pounds of waste from landfills.”
Glenn Hasek can be reached at greenlodgingnews@gmail.com.