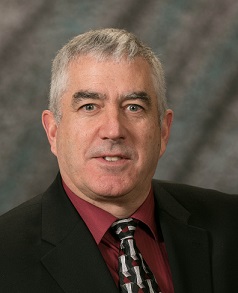
Hotels, motels and other lodging facilities frequently wash thousands of pounds of sheets, towels, pillow cases and other linens each day. While just 8 to 12 percent of the laundry operation represents initial equipment costs, a staggering 87 percent of the total laundry budget consists of operating costs: water, chemicals, electric, gas and labor. For lodging entities embracing green and other technologies to reduce costs, the laundry operation should be a focal point.
Reducing Water Use
While today’s commercial washer-extractors are far more efficient than decades ago, manufacturers continue to fine tune operation. More innovative manufacturers have designed special spray heads and accompanying software to reduce the quantity of water needed to effectively wash and rinse laundry. For example, spray-rinsing technology is a highly effective way to pull wash chemistry through the load and eventually down the drain. This new technology allows the laundry machine to consume 39 percent less water than other commercial laundry machines that utilize conventional bath rinses. Further, cycle times are reduced by up to 12 percent (because the machine does not need to fill the wash cylinder for each rinse), which increases throughput. From a green perspective, the benefits not only include decreased water use, but related reductions in electricity.
Reducing Electrical, Gas & Labor Cost
Up to 79 percent of on-premises laundry (OPL) professionals believe that each load of laundry is over-dried by an average of eight minutes per cycle. In a 75-pound tumble dryer that can mean an unnecessary $883 in annual utility costs.
Over-drying has other costs, too, and those are somewhat hidden. One of these is unoptimized labor. Often, laundry staff are idle while waiting for a load to fully dry, when they could otherwise be folding or storing laundry—or engaging in other laundry-related tasks. Determining when a load is dry becomes a haphazard guessing game. Finally, over-drying leads to fiber degradation in the linens themselves, significantly reducing their service life. The lint you pull out of your tumble dryer is coming from those linens—longer drying means more wear and tear, more lint and reduced linen life.
New innovations in the market, however, can mitigate the utility and labor costs associated with over drying. Laundry managers seeking ultimate efficiency will want to look for over-dry prevention technology that utilizes greater contact area for a higher degree of accuracy. These systems dry to the desired moisture level and stop the unit. That efficiency can be taken further if the technology is paired with a step-drying approach. In these units, high heat is used early on (when loads contain the most moisture) until the load is half-dry. Temperatures are then lowered during the remainder of the cycle until the load reaches the pre-set residual moisture level. Step-drying helps reduce gas and/or electric consumption. A major benefit of the highly-accurate sensors is they take the guess work out of determining dryness levels and allow the laundry professional to use time more efficiently. Taking the 8-minute over-drying estimate from laundry professionals at face value and using a 75-pound dryer unit in the equation, a laundry operation could save up to $4,866 in unnecessary labor costs per year.*
Leveraging Laundry Machine Innovations with Intelligent Technology
The adage, “You can’t improve what you can’t measure” holds true in the hotel OPL operation. Fortunately, the same electronic intelligence found in the auto and electronics industries is becoming part of some cutting-edge models—and it’s never been easier to view and analyze the data to reduce overall operation costs.
Some systems today network washer-extractors and tumble dryers. They can monitor one machine, all the machines in a laundry room, or even multiple machines in laundry rooms across a large enterprise, e.g. a hotel chain across North America. It provides visibility to key performance indicators that affect overhead, including labor and utility costs. As noted earlier, operating costs account for 87 percent of the laundry budget. Thus, even small adjustments can result in significant annual savings. The downside has always been getting operators to use the information. No longer.
Hoteliers seeking to leverage such systems will want to place a premium on ones that are user-friendly. Ease of use simplifies setup for laundry managers and gives quick access to key data. Managers use a simple interface to upload factors like labor and utility costs. The system then calculates and keeps management updated on key metrics like capacity utilization, productivity (measured in pounds processed), and utility and labor costs. The outcome is a measure expressed in terms of “efficiency” which shows the aggregate cost per pound of laundry processed.** With Cloud-based functionality, the information can be accessed from anywhere in the world via PC, tablet or smart phone. Again, the usefulness of such systems is determined by how quickly managers can read an act on information to they should look for systems that present data in simple, graphical dashboard-style reports. Such dashboards are perfect for sharing up to general managers and other management. Operators can view laundry efficiency at several levels including machine, location or several laundry room locations.
Data gives management or operators the power to make immediate adjustments that can significantly affect the bottom line and finished quality. It also allows the operator to set internal benchmarks to guide productivity in terms of efficiency. Management also can compare efficiency levels from one shift to another and from one operation to another, across an enterprise.
Negotiating the Labor Shortage
Finding reliable labor in the laundry industry (and in general) has become an endemic challenge. For the first time, there are more job openings than there are eligible workers to fill them. Indeed, Manpower Group reported in 2018 that 46 percent of companies are finding it difficult to find labor. Yet, labor accounts for a significant portion (45 to 50 percent) of operating costs in the laundry operation. Thus, getting the maximum efficiency out of each machine, and the extended laundry operation is becoming critically important.
Tying it all Together
With the current labor shortage, and increasing pressure within organizations to use labor effectively, the case for increasing laundry room efficiency seems logical. The latest technologies and reporting not only help reduce utility and chemical costs, they can also optimize labor hours. The potential savings in annual operating costs alone (labor, utilities, linens and chemicals) can easily outweigh an investment in one or more new machines. In addition to the overall cost savings associated with adopting new laundry technologies, it complements organizations embracing a green operational strategy.
*Based on seven days/week and $10/employee hour
**Machine-related labor only—not folding, transport, etc.
Bill Brooks is the national sales manager for UniMac, a leading provider of on-premises laundry equipment. He can be reached at bill.brooks@alliancels.com or (920) 748-4437.